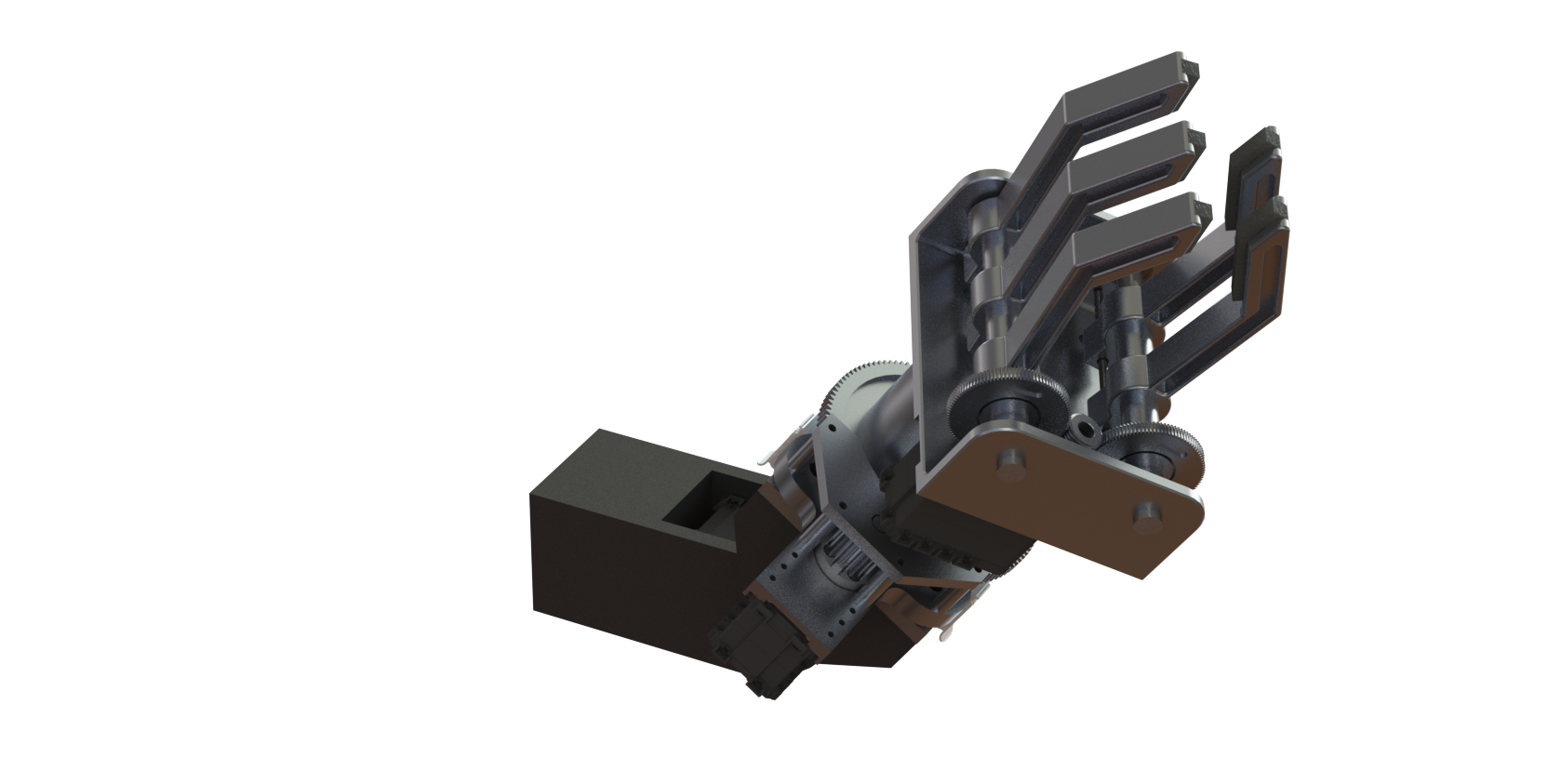




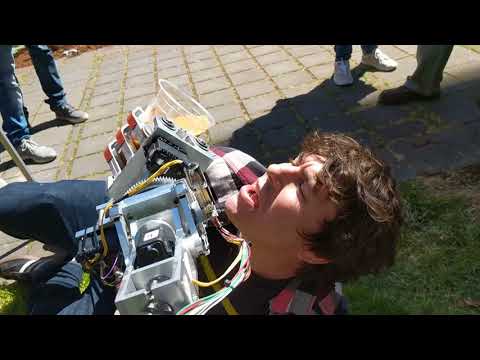
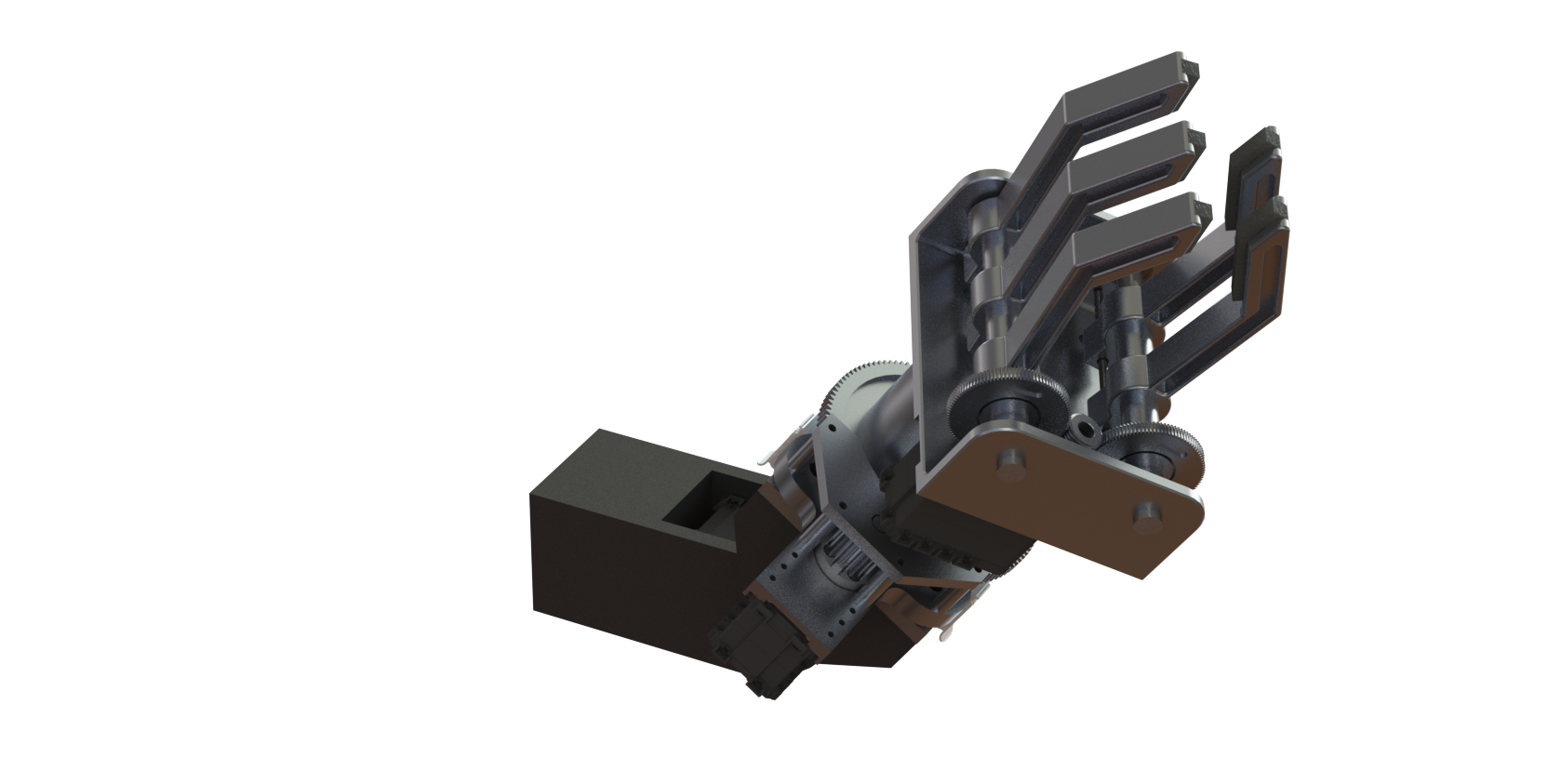
I was one of three engineers to design, manufacture, and assemble this end effector for the 2016 - 2017 OSU Robotics Club Mars Rover. The overall design was not what you would call a traditional end effector, but we decided to take a risk and go with a design that hadn't been attempted before. When it came time to compete, it paid off. In fact, in the events that it was designed specifically for, this end effector got us the highest score of all the teams that competed.

The design on this end effector is simple. The fingers are opened and closed via a worm that turns two gears attached to the rods that the fingers are mounted to. The fingers are split into two pieces, an upper and a lower half. The lower half stays on the rods and are axially located and fixed using setscrews. The upper halves can be switched out for shorter or longer fingers, depending on what the competition calls for.
The worm is driven with an ax-12 servo, as is the gear that controls the roll. The roll is infinite, which is possible because of our use of a slip-ring and an igus slewing bearing.
The end effector was made to compete in an event that would require the robot to lift a container of liquid weighing 5 kg, pull a cart for ~50 feet, and then open a tank, empty the liquid into the tank, and then close the tank. This proved very challenging, and our team was the only one that was capable of the agility that the event required. We got first place in that event (89/100), and the second place team was over 20 points behind us.

We got the upper and lower finger sections machined by the fine folks at GrayGo Industries in beautiful Junction City, Oregon.

GrayGo was also kind enough to machine the bracket that housed the inner workings of the end effector. This was an absolute lifesaver, as we would have had to split the part into three pieces, machine each piece individually, and bolt it all together. This would have been a much weaker part and we're very grateful to GrayGo for their help.

Here is the completed end effector with the short fingers attached and opened as widely as possible. It is mounted to the end of the arm and is ready for competition.
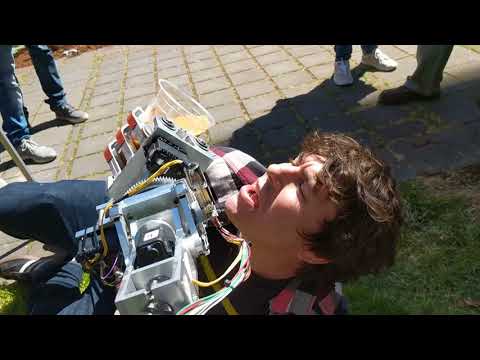
I believed in my robot so much, I allowed it to pour iced coffee into my mouth while we were tabling for a College of Engineering event. Not a drop was spilled on my clothing or person!